Industria 1, 2, 3, 4... y 5.0
Nexans adapta sus datos a las operaciones comerciales

Se está produciendo un cambio. Muchos países, entre ellos Estados Unidos y Francia, están abandonando la economía sin fábricas -el modelo dominante en los últimos treinta años- para redescubrir las ventajas de fabricar en casa. Este cambio crea una oportunidad única para promover el desarrollo de fábricas de nueva generación, que reflejen los nuevos retos económicos, sociales y medioambientales. Lo local por lo local ha sido siempre la consigna de Nexans, que aprovecha esta oportunidad para dar un nuevo paso adelante en su desarrollo. Integrando su riguroso modelo de gestión con su base de producción internacional, la empresa estará en modo industria 4.0 en 2025.
Cuando hablamos de la revolución digital, tendemos a pensar primero en el exceso de información que inunda nuestras vidas, cada día de cada semana, anunciando un nuevo y revolucionario teléfono inteligente, un novedoso robot de cocina o los últimos y alucinantes avances en inteligencia artificial (IA). Es un tema que solo recientemente ha pasado al primer plano en el mundo de los negocios, con el encendido debate en torno al impacto de la IA en las actividades empresariales y la rápida automatización que se espera en muchos ámbitos, desde la programación a la contabilidad, la medicina y el Derecho.
Paradójicamente, la industria ha suscitado mucho menos interés como tema de debate. Y, sin embargo, es una temática de importancia clave, no solo en términos de empleo, innovación y creación de valor, sino también de soberanía. La pandemia de COVID-19 fue una llamada de atención para los países europeos, que tomaron conciencia de la magnitud de su dependencia económica y estratégica, a la luz de las tensiones entre China y Estados Unidos. Las fábricas tienen un papel clave que desempeñar en la adaptación de nuestras economías al nuevo orden tecnológico.
Cómo la industria se reinventa con la industria 4.0
Esto no es de extrañar, ya que los cambios en los talleres siempre han ido de la mano de avances tecnológicos, continuando un ciclo que comenzó con dos revoluciones industriales. A la máquina de vapor y las primeras fábricas siguieron la llegada de la electricidad, las máquinas-herramienta y la producción en serie, y después, en los años 50, la electrónica, la automatización mediante programación, las máquinas de control numérico, los robots industriales y los primeros paquetes de software de supervisión.
La cuarta revolución, actualmente en desarrollo, continúa directamente el proceso de informatización en curso, al tiempo que lo lleva a un nivel completamente nuevo. El primer paso es establecer una nueva base energética, alejándose de los combustibles fósiles que impulsaron las tres revoluciones anteriores. El segundo paso consiste en maximizar el uso de un nuevo recurso clave —los datos empresariales— basándose en una potente combinación de alta tecnología que ya ha alcanzado la madurez: infraestructuras de muy alta velocidad (fibra para conexiones fijas y 5G para móviles), combinadas con alojamiento de datos y procesamiento masivo (nube, macrodatos, IA), inteligencia descentralizada y objetos inteligentes (IdC) y nuevas formas de interacción hombre-máquina (realidad mixta, gemelos digitales, avatares).
Esta avalancha de innovaciones está sentando las bases para un replanteamiento completo de la forma de trabajar de las empresas, con especial énfasis en todos los procesos que intervienen en la producción. Para muchas potencias industriales, se ha convertido en una prioridad. No es casualidad que Alemania fuera la primera en lanzar un plan de Industria 4.0 en 2011, con la vista puesta en mantener la excelencia de su base industrial. Persiguiendo el mismo objetivo, China está invirtiendo en fábricas de alto valor añadido para conservar su poderío industrial y hacer frente a una creciente escasez de mano de obra. Francia adoptó una estrategia similar en 2015, con su Alliance for the Industry of the Future, una asociación de 32 000 empresas que se reúnen cada año en la feria Global Industry. Este año, Nexans fue el centro de atención al conseguir dos premios Golden Tech en las categorías de Diseñador y Fabricante en la edición de 2023, celebrada el pasado mes de marzo en Lyon (Francia).
Nexans 4.0 rumbo a 2025
Estos objetivos forman parte de un nuevo compromiso que implica a todos en Nexans. El Grupo avanza hacia la integración digital global de todas las áreas de la empresa y su ecosistema con el fin de simplificar los procesos, mejorar el rendimiento y la respuesta, impulsar la productividad y la seguridad y limitar las operaciones innecesarias, así como anticiparse y planificar los acontecimientos (mantenimiento predictivo, gestión de inventarios, satisfacción del cliente, etc.).
En una reciente encuesta realizada a empresas francesas, el 98 % de las compañías destinatarias afirmaron que ya han planificado o desplegado iniciativas relacionadas con la Industria 4.0 (7.ª edición del barómetro Wavestone sobre Industria 4.0, realizado en colaboración con Bpifrance y France Industrie). Las principales motivaciones citadas son el rendimiento industrial (para el 30 % de los encuestados) y el control de los datos (27 %). Obsérvese que el impacto ecológico y el rendimiento energético ocupan este año el tercer lugar (15 %).
El Grupo Nexans dio el primer paso hacia el cambio a finales de 2020, cuando se asoció con Schneider Electric, una empresa con experiencia demostrada en la transformación de su propia base industrial. El proceso iniciado por Schneider Electric hace hincapié en la fiabilidad, la productividad, la mejora de la disponibilidad mediante el mantenimiento predictivo, la eficiencia energética y la protección contra los ciberataques. La primera fase de la asociación consistió en importantes inversiones en centros piloto de Autun (Francia) y Grimsås (Suecia). El proceso se desplegará en ocho plantas más a finales de 2023, con el objetivo de modernizar las 45 plantas del Grupo en cuatro continentes a finales de 2025, a un ritmo de entre 12 y 15 plantas cada año.
Estos cambios fundamentales implican la movilización de los datos del Grupo: la materia prima de esta nueva revolución industrial. Aunque la proporción de datos utilizados por el Grupo pasó del 5 % al 10 % entre 2019 y 2023, el objetivo es alcanzar el 70 % en 2026.
“ Estamos abordando la transformación digital del Grupo en dos niveles, en primer lugar integrando las nuevas tecnologías en nuestras operaciones y, en segundo lugar, creando un entorno colaborativo. ”
Vincent Dessale
Director de Operaciones de NexansEste enfoque conecta las herramientas de producción utilizando recursos del IdC y la IA, al tiempo que permite a los empleados recuperar el control a través de cuadros de mando, indicadores de apoyo a la toma de decisiones y la supervisión de la calidad y la seguridad. También contribuye a reducir el tiempo de respuesta y de comercialización.
Recuerde activar los subtítulos en español para el vídeo en los ajustes
Razones para una revolución: qué cambia realmente sobre el terreno
En primer lugar, observaremos cambios en nuestra forma de trabajar cada día. Porque la transformación no tiene que ver solo con la tecnología, aunque las máquinas conectadas y los robots movidos por IA son algo cada vez más habitual en las fábricas, junto con las carretillas elevadoras automáticas que recorren los pasillos de los centros logísticos día y noche. Sin embargo, los cambios más espectaculares afectan a los trabajadores humanos, con talleres repletos de pantallas, tabletas y gafas conectadas.
Se trata de un tema delicado, ya que el éxito de la transformación dependerá de la capacidad de las personas para trabajar junto a las máquinas. Este es precisamente el objetivo de la Industria 5.0, como a veces se la denomina. La meta es ampliar y reforzar la transformación digital apoyando una mejor colaboración entre las personas y las máquinas, sin olvidar la creatividad y el bienestar.
Este aspecto se tiene en cuenta desde el principio en el proyecto de Nexans:
- Los cuadros de mando en tiempo real controlan el correcto funcionamiento de las líneas de producción, actualmente en cada planta y pronto en toda la base industrial global del Grupo. La supervisión de los datos en tiempo real aumenta el rendimiento industrial y el control de la calidad, al tiempo que reduce el consumo de energía y materias primas y recorta los costes energéticos en un 15 %.
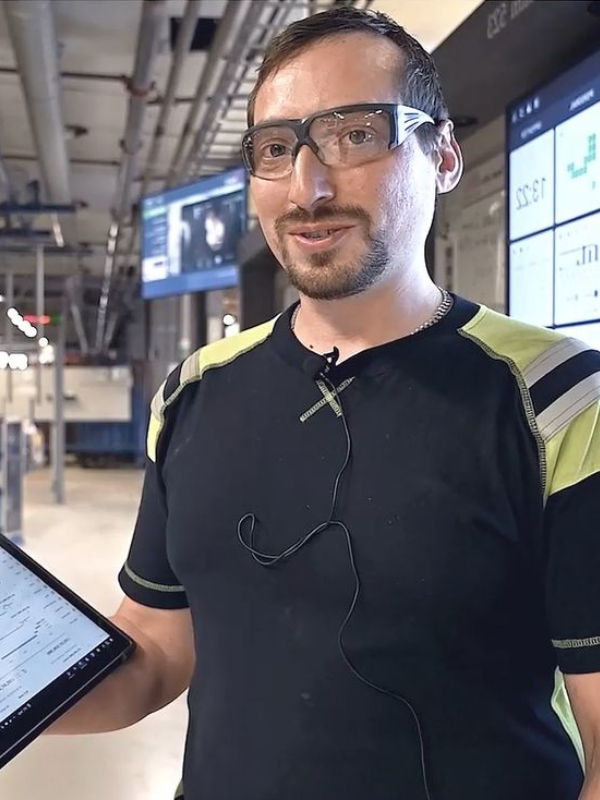
- Una red social empresarial permite a los operarios acceder a módulos en vídeo y tutoriales, así como a un foro de chat. El foro tiene un valor incalculable para debatir las mejores prácticas y encontrar soluciones rápidamente, ya que los usuarios pueden enviar sus preguntas directamente a la comunidad en línea. También, es una forma de realizar un seguimiento de las acciones pasadas, lo que contribuye a que los operarios, el personal y la dirección compartan información y a que las operaciones cotidianas se desarrollen sin contratiempos, mientras ayuda a los trabajadores a ser más autosuficientes.
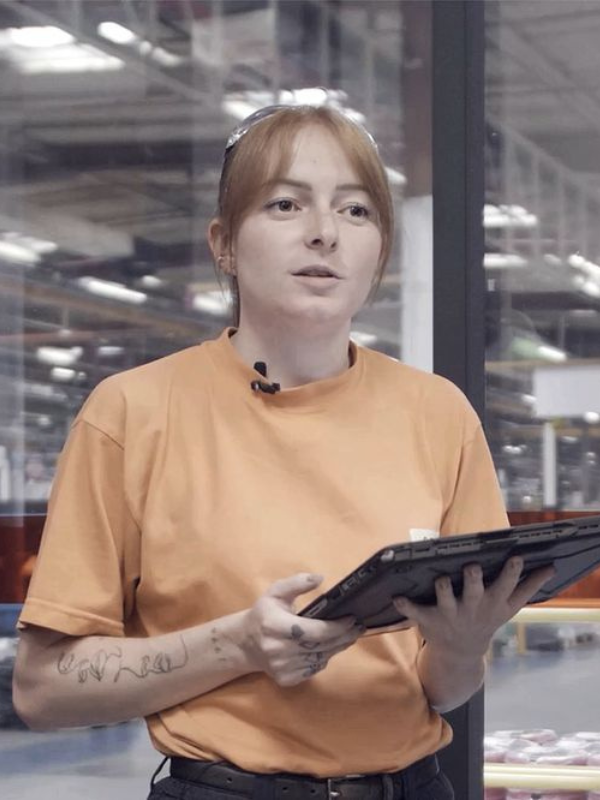
- Las gafas conectadas se utilizan para reducir el estrés en el lugar de trabajo, estableciendo una línea directa entre expertos y operarios en cualquier momento, para gestionar fases de producción delicadas o problemas de producción urgentes, mediante el uso de la realidad aumentada.
En esta etapa clave del proceso, el objetivo es que la digitalización libere a los operarios del trabajo repetitivo, para que puedan centrarse en tareas de mayor valor añadido. La transformación digital también desempeñará un papel en el aumento del atractivo de nuestro negocio para la generación más joven, nativa digital, al tiempo que creará oportunidades para que diversifiquemos los perfiles laborales, reduzcamos el tiempo trabajando en las máquinas y mejoremos las capacidades a través de programas de formación adecuados.
Para aprovechar todo su potencial, este nuevo enfoque de la gestión de la base de producción debe integrarse con los objetivos estratégicos de la empresa. Llevando este proceso lo más lejos posible, Nexans se está asegurando de que su plan de industria 4.0 sea coherente con el modelo de gestión E3, apuntalando la transformación del grupo mediante el apoyo de los objetivos de rendimiento económico, ventajas medioambientales y compromiso de los empleados.
Lionel Fomperie, Director de Estrategia Industrial del Grupo, y Thomas Wagner, Director de Rendimiento de SI, ofrecen una visión general del programa y explican cómo Operaciones colabora con TI/OT para generar plataformas de TI/OT y Ciberseguridad.
Recuerde activar los subtítulos en español para el vídeo en los ajustes
Lionel Fomperie, Director de Estrategia Industrial del Grupo, Chao Li, Ingeniero de Desarrollo Digital y Olivier Ameline, Director de Nexans Excellence Way nos conducen a través de tres casos de uso: Unified Operation Cockpit (UOC), MES Performance (Manufacturing Execution System) y SQDCE Digital board: S de Seguridad, Q de Calidad, D de Retraso, C de Coste y E de Medio Ambiente.
Lionel Fomperie, Director de Estrategia Industrial del Grupo, Chao Li, Ingeniero de Desarrollo Digital y Olivier Ameline, Director de Nexans Excellence Way nos conducen a través de tres casos de uso: Unified Operation Cockpit (UOC), MES Performance (Manufacturing Execution System) y SQDCE Digital board: S de Seguridad, Q de Calidad, D de Retraso, C de Coste y E de Medio Ambiente.
Recuerde activar los subtítulos en español para el vídeo en los ajustes
El programa de transformación digital apoya a nuestros operarios y les hace la vida más fácil facilitando el acceso a todos los documentos necesarios y apoyando la producción remota.
Descubra con Chao Li, ingeniero de desarrollo digital, y Mylène Iller, operaria de producción en Autun (Francia), cómo se facilita la vida de los operarios.
Recuerde activar los subtítulos en español para el vídeo en los ajustes
Descubra con Chao Li, ingeniero de desarrollo digital, y Tobias Karlsson, operador de mantenimiento predictivo en Grimsås, cómo se ha puesto en marcha el mantenimiento predictivo en nuestra fábrica sueca. El objetivo es monitorizar los principales indicadores de producción como temperatura, presión, tracción, para detectar la evolución en las tendencias de estos parámetros.
Descubra con Chao Li, ingeniero de desarrollo digital, y Tobias Karlsson, operador de mantenimiento predictivo en Grimsås, cómo se ha puesto en marcha el mantenimiento predictivo en nuestra fábrica sueca. El objetivo es monitorizar los principales indicadores de producción como temperatura, presión, tracción, para detectar la evolución en las tendencias de estos parámetros.
Recuerde activar los subtítulos en español para el vídeo en los ajustes
Nuestros sitios web
Selecciona tu país para conocer nuestros productos y soluciones
-
Africa
- Africa
- Ghana
- Ivory Coast
- Morocco
- North West Africa
- Americas
- Asia
- Europe
- Oceania